Circular economy: the integrated waste treatment solution breaking new ground in Yorkshire
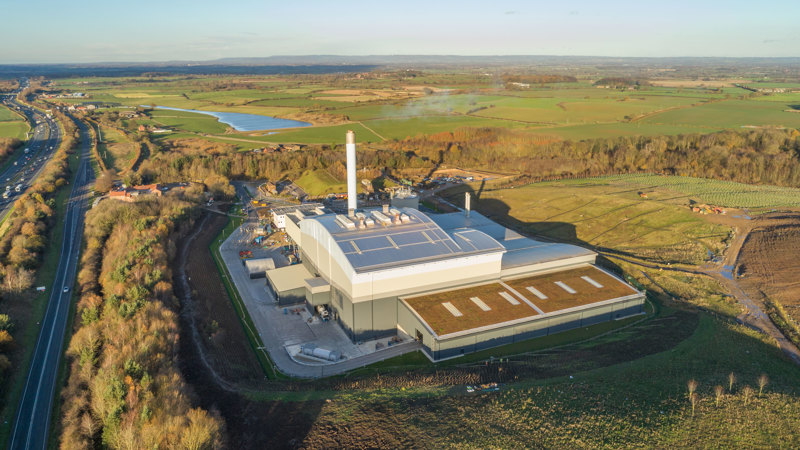
Ten years ago, as many UK councils grappled with reducing the amount of waste going to landfill, North Yorkshire and York put their faith in an innovative idea. The result is the UK’s first 3-in-1 waste plant. Managing Director, Paco Hevia shares the journey.
Allerton Waste Recovery Park makes a majestic impression as you drive north on the A1 through North Yorkshire, its gleaming structure emerging like a silver wave behind the trees. But that could just be me. I’ve been working on the project since we first put pen to paper in 2008 and I am perhaps a little too attached.
AWRP is unique in the UK for integrating three processes for the treatment of residual waste - mechanical treatment, anaerobic digestion and energy from waste (EfW) – and co-locating them on one site as a single installation.
The first maximises recycling, the second transforms organic matter into biogas and the third recovers from the remainder more than enough power for a town the size of Harrogate. It’s a successful example of 21st century circular economy in a traditionally rural environment.
Conceived on behalf of North Yorkshire and City of York councils as a solution for turning 320,000 tonnes of ‘black sack’ household waste a year into a resource instead of sending it to landfill, AWRP has weathered many challenges on the ten-year road from inception to full commissioning earlier this year. Yet through several iterations its design has remained state-of-the-art.
Innovative technology and funding solutions
First, a little bit about the technology. With 25 years of service delivery post commissioning to look forward to, we needed technology that was innovative, flexible, resilient and gave us adequate control over performance.
We opted for a combination of treatment technologies to allow us an opportunity to improve the recycling performance of both councils while at the same time controlling the quality and calorific value of the residual fraction delivered to the EfW facility.
All residual household waste is processed mechanically to separate out the recyclable materials (different metal and polymer fractions) for reprocessing into new products.
Organic materials, such as food and garden waste, are also separated in the mechanical process and diverted into the second stage; an anaerobic digester where they are used to generate a methane-rich biogas which is used as fuel in two large gas engines to generate around 1 MWe of green energy.
The residue from digestion along with non-recyclable and materials with no current viable recycling market end up in the EfW plant. Here it is burned above 850C and we recover the energy through a steam cycle to power a turbine to generate 218GWh of electricity per year.
Emissions are treated and controlled by a comprehensive filter system to comply with environmental permit limits, while the combustion ash – around 70,000 tonnes a year - gets turned into construction-related materials for use on highways and infrastructure projects.
Overcoming the challenges
Delivering an asset which is as state-of-the-art now as when it was conceived in 2008 involved talent and expertise across a range of disciplines. A lot can happen to funding markets, technological advances and Government policy over the course of a decade.
For Allerton, the challenges included a highly complex and expensive planning process plus pressure on funding costs through the credit crunch and subsequent austerity measures.
With an integrated team including investment specialists and technical experts, we helped bring new funding solutions and value-engineering on board to evolve the solution from a central Government funded PFI into an affordable and successful Public Private Partnership still delivering all the original objectives of the councils promoting it.
The commercial and financial simplification of having a single management team also helped us make nimble and pragmatic decisions on value, to the extent that, even during the construction phase, we continued to optimise the solution and keep abreast of developing technology.
A new way of thinking and delivering
At its heart, Allerton is a pragmatic value for money solution allowing both councils to reduce expenditure on the disposal of waste whilst having a positive impact on the environment and climate change by drastically reducing the carbon footprint of waste management in North Yorkshire.
It also allowed the councils to move up the waste hierarchy by increasing recycling by 2.5% and reducing landfill disposal by a minimum of 90%, while generating local employment opportunities and increased potential for investment by other industries.
Unlike many projects where the design, build and operation of assets are carried out by separate companies, our approach was to oversee and manage the creation of a comprehensive integrated solution through the life of the project, wrapping and coordinating all aspects of the design, planning, delivery, financing and operation.
In a market where most waste operators did not normally have the full range of funding, design, engineering and procurement capabilities, the idea of managing all project risks under one roof in combination with a disruptive integration of technologies on a single process, including an innovative approach to anaerobic digestion for residual waste fines, became a real differentiator.